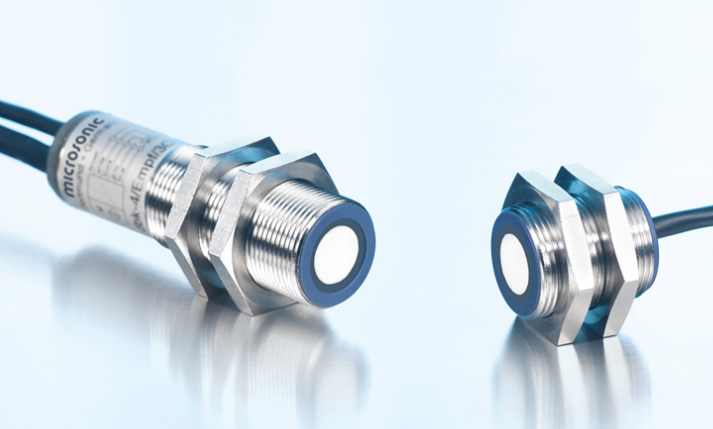
Model: dbk+4/M12/3BEE/M18 E+S dbk+4 double sheet detector MICROSONIC Vietnam
Hãng sản xuất: Other Brands
Model: dbk+4/M12/3BEE/M18 E+S dbk+4 double sheet detector MICROSONIC Vietnam, Đại lý Model: dbk+4/M12/3BEE/M18 E+S dbk+4 double sheet detector MICROSONIC Việt Nam, Hàng Sẵn Kho Piteco, Máy dò tờ gấp đôi MICROSONIC Vietnam
100% Germany Origin |
MICROSONIC Vietnam |
Model: dbk+4/M12/3BEE/M18 E+S |
Description The task of double-sheet control is to identify two or more pieces or sheets inadvertently adhering together. The functional principle A high-frequency ultrasonic transmitter beams against the sheet from the underside. The beamed signal induces the material to vibrate. The effect of these vibrations is a very small sonic wave on the other side of the sheet being spread. This wave is evaluated by the ultrasonic receiver on the opposite side. The signal from the stacked sheet ("double sheet") is so weak that it hardly gets to the receiver. The dbk+4 detects missing, single and double sheet. Functional principle The working ranges The new dbk+4 has 3 control inputs by means of which 3 working range can be preselected. The standard working ranges covers the sheet material weight range from 20 g/m2 to 1,200 g/m2. Extremely thin materials such as Bible printing paper with a weight per unit area of less than 20 g/m2 are scanned with the use of the "Thin" setting. The "Thick" setting is available for paperboard containers and fine-corrugated card. Changes between the working ranges can be undertaken under on-going operations. A Teach-in for the material to be scanned is not necessary. If the 3 control inputs stay unconnected, then the dbk+4 operates in the standard working range. As such, a very broad material spectrum can be scanned. Teach-in The Teach-in function is additionally available for materials which cannot be scanned with one of the three working ranges. A material Teach-in is done by inserting a single sheet into the double-sheet control. The C3 control input is then placed to logic 1 level for at least 3 seconds. Materials with non-homogeneous elements must be moved during the Teach-in phase so that the dbk+4 detect them. Success with a Teach-in operation is shown by a green LED. The material can now be scanned. The Teach-in makes it possible to scan material from thin Washi to wafers glued with a water film. Range of uses of dbk+4: Sheet-printing machinesdbk+4 ultrasonic double-sheet control Assembly machines Folding machines Paper-processing machines Manufacturing of solar cells and silicon wafers Labelling PCB manufacturing Paper, Film, Sheet material The mounting The recommended spacing between transmitter and receiver is 40 mm (or 20 mm with dbk+4/M12/CD/M18 ER+S). If needed, this spacing can be adapted to the local conditions in the 20 to 60 mm range. For the matter of commissioning, this can be done by means of a simple Teach-in or with the LinkControl parameterisation software. Double-sheet control Material-conditioned fitting position With papers and thin films, the double-sheet control is effected perpendicularly to the material; flapping does not impair the function. In the case of fine-corrugated card, thin sheet metal, wafers or thicker plastic films (e. g. credit cards), the dbk+4 should to be mounted at a specific angle of inclination α to the material running through